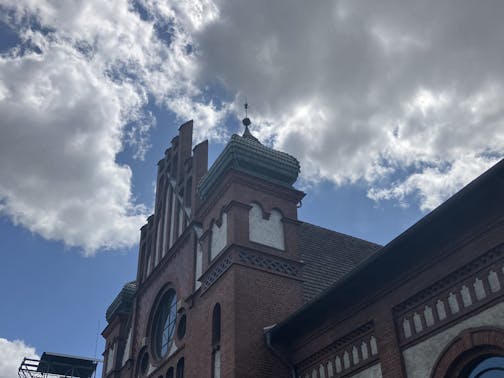
White sneakers, please!
Let's go on a tour of Zalando's logistics center with Operations Manager Hamid Tabar - from Inbound to Outbound.
by Nora Smets
3 min
26 September 2022
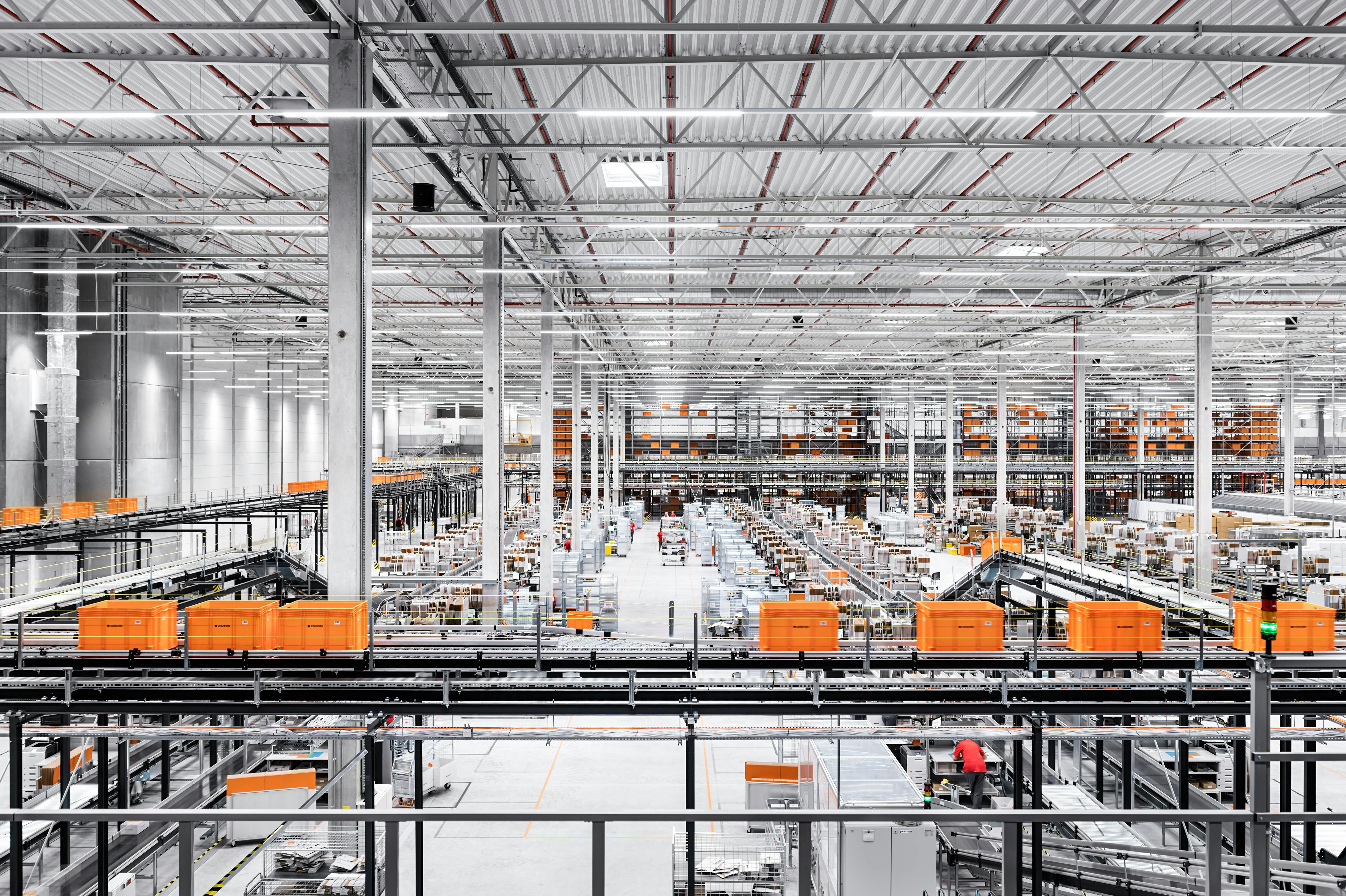
There's something about a bright white sneaker. They are ordered from Zalando many thousand times a day. But which stations does a sneaker actually pass through in our logistics centre? Come with us on a quick tour - from the delivery of the shoe up to the shipping to one of our 48 million active customers.
Starting with the delivery
Piles of pallets. As far as one can see. Employees in yellow high-visibility waistcoats move between them. They check papers, scan information and throw hand signals to the waiting truck drivers at the gates. What happens here? "All the items that Zalando orders from the manufacturers arrive at the Inbound department," Hamid explains. "The employees make sure that the goods are delivered to the site in the right quantities and in the right quality.”
Stopver: Receive and Stow
In the "Receive" area, the goods are unpacked. Today: a whole pallet of white sneakers. Then the team sticks a yellow sticker on each shoe. "Now the shoe is registered in the logistics centre and we know where it is at all time," says the 31-year-old operations manager, while his colleagues put the freshly labeled sneaker into orange tubs.
A conveyor belt, which is several kilometres long, takes the tubs to the next station: the tub station in the "Stow" area. This is where our stowers store the goods. At first glance, the warehouse appears chaotic. Sunglasses lie on the shelf right next to pumps and boxer shorts. Hamid, a career changer with a degree in marketing/international business, explains: "The chaos makes the storage efficient. We save storage space, don't lose time by sorting systematically and shorten the walking distances of our colleagues.”
And now? Going to Pick!
As soon as a customer orders online at Zalando, the work begins for our pickers. With a shopping trolley and a navigation device, they move through the aisles and collect all the products ordered. And bang, there it is! Our white sneaker at storage location 01-100-101-A. "You already know what happens next: the picked items go back into an orange tub, onto the conveyor belt and off to 'Sort'”, Hamid explains to us.
Getting faster - on our way to Sort and Pack
As the name suggests, in the "Sort" department employees sort the products, because the tubs contain the orders of many different customers. As soon as all the items are assigned to the right order, it's time to pack. In "Pack", the packers check whether the orders are complete. Then they choose the right box size or shipping bag. "Of course, this is sustainable, space-saving and secure with the help of a computer system," Hamid adds. As soon as an order is packed, the package travels via conveyor system to "shipping". Soon it's off to the customers - for our white shoes, too.
Finally, we arrive at Shipping
In the shipping department, our logistic employees wait for the finished packages. They slide down conveyor belts towards a truck trailer. Now they are stacked to save space: "It's a bit like playing Tetris," Hamid smiles and checks that the package with the desired shoes has a safe place. And then: the trailer is full, the team secures the load and the bright white sneakers are on their way to the customer.